MTI PCBA’s Expertise Unveiled: Pioneering the Future of Sleep with MindLax
In today’s fast-paced world, quality sleep is a precious commodity that many struggle to obtain. Recognizing the importance of restful nights, MTI PCBA has taken the lead in pioneering an innovative sleep solution: the MindLax Sleeping Mat. This revolutionary tool, engineered from the ground up by MTI PCBA’s experienced team, promises to transform the way we approach sleep.
The Birth of MindLax
Quality sleep is a fundamental component of our overall well-being, impacting our physical health, mental acuity, and emotional stability. With this understanding, MTI PCBA embarked on a journey to develop a groundbreaking sleep aid that would revolutionize the way we experience rest.
MindLax emerged from the fusion of cutting-edge technology and scientific understanding of sleep patterns. At its core, it utilizes aviation-grade special rare metal materials and pairs them with digital content and a sophisticated algorithm to optimize its effectiveness.
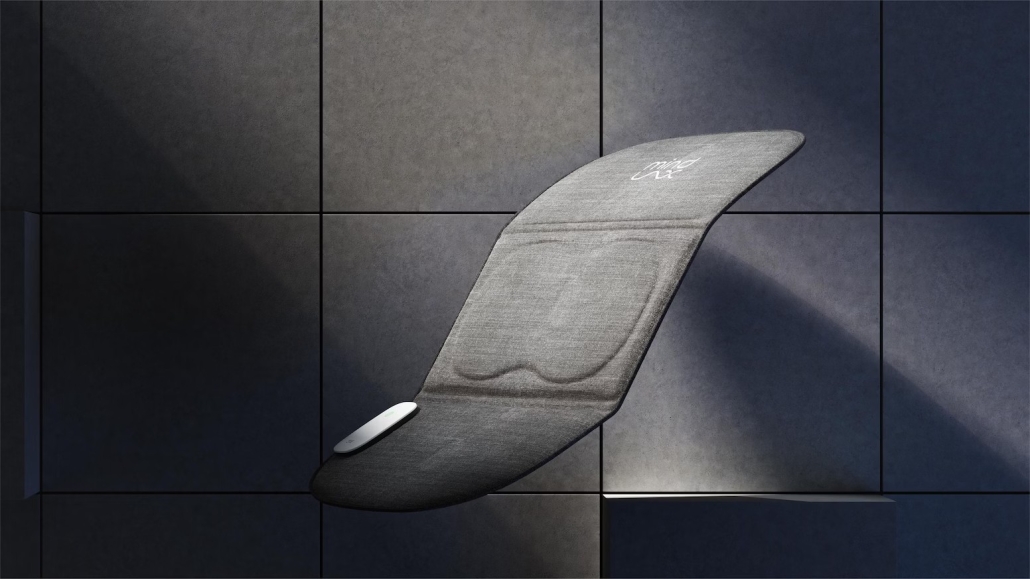
MTI PCBA’s Role in MindLax’s Journey
MTI PCBA is the driving force behind the creation of MindLax, taking charge of every stage of development, from inception to mass production. Let’s delve into the remarkable capabilities and experiences that make MTI PCBA the ideal partner for such an ambitious project.
1. Schematic Design: The Blueprint for Innovation
The journey began with the creation of a comprehensive schematic design that laid the foundation for MindLax’s exceptional capabilities. MTI PCBA’s team of skilled engineers meticulously crafted the blueprint, ensuring that every component would seamlessly interact to achieve the desired sleep-enhancing effects.
2. PCB Layout: Precision in Every Detail
The printed circuit board (PCB) is the nervous system of MindLax, connecting its various components and facilitating communication. MTI PCBA‘s expertise in PCB layout was instrumental in designing a compact yet efficient board that maximized MindLax’s functionality while maintaining user comfort.
3. Firmware Development: Bringing MindLax to Life
MindLax’s capabilities extend beyond hardware. Its firmware, developed by MTI PCBA‘s proficient team, enables seamless operation and synchronization of its multi-frequency waveguide system. The firmware’s efficiency ensures that users can harness MindLax’s potential effortlessly.
4. Prototyping: Iterative Perfection
Before unveiling the final product, extensive prototyping was necessary to fine-tune MindLax’s performance. MTI PCBA‘s commitment to perfection drove a series of iterations and improvements, resulting in a sleep aid that consistently delivers on its promises.

PCBA
5. Mass Production: Scaling Sweet Dreams
MTI PCBA’s ability to transition from prototype to mass production is a testament to its manufacturing prowess. This transition ensures that MindLax is readily available to help people worldwide experience the benefits of improved sleep.
MindLax’s Unique Features
Central to MindLax’s effectiveness is its Multi-frequency Waveguide System, which incorporates two essential elements: Neuro TIM™️ and Neuro Arc™️. Together, these components transmit sleep-enhancing sounds and vibrations directly to the brain, bolstering the production of Alpha brain waves—a key factor in achieving high-quality sleep.
– Neuro TIM™️: The Brainwave Maestro
Neuro TIM™️ is the conductor of MindLax’s symphony of sleep. Through carefully crafted soundscapes and vibrations, it orchestrates the brain’s Alpha wave production. These Alpha waves are instrumental in achieving deep relaxation and fostering a tranquil state of mind conducive to restful sleep.
– Neuro Arc™️: The Path to Rapid Relaxation
Neuro Arc™️ complements Neuro TIM™️ by ensuring rapid and profound relaxation. Its innovative approach leverages advanced algorithms and digital content to guide users into a state of deep relaxation swiftly. This groundbreaking combination sets the stage for restorative sleep.
The Future of Sleep with MindLax
The introduction of MindLax marks a significant milestone in the quest for improved sleep quality. MTI PCBA‘s unwavering commitment to innovation, precision, and excellence has culminated in a product that promises to redefine the way we sleep.
As MindLax continues to gain recognition for its transformative effects, it also serves as a testament to MTI PCBA‘s capabilities and dedication to pushing the boundaries of what is possible in the world of electronic design and manufacturing.
In conclusion, MindLax represents a harmonious union of technology, science, and ingenuity, with MTI PCBA as its visionary architect. Together, they have created a sleep solution that empowers individuals to unlock the full potential of restful nights, contributing to healthier, happier lives.
Discover the future of sleep with MindLax—a testament to MTI PCBA‘s passion for innovation and excellence.